In semiconductor manufacturing, the environmental control and air quality management in wafer fabs (Fabs) are one of the key factors to ensure product quality and production efficiency. As an important part of the Heating, Ventilation and Air Conditioning (HVAC) system, chemical filters play a crucial role in wafer fabs. This article will conduct a detailed analysis of the application, function, design considerations and impacts of chemical filters in Fab chip wafer fabs.
I. Introduction
With the rapid development of the semiconductor industry, the requirements for the production environment in Fab chip wafer fabs have become increasingly stringent. Among the many factors affecting the production environment, air quality plays a key role in the stability of the chip manufacturing process and the product yield rate. As an important device for ensuring the air quality in wafer fabs, the application and function of chemical filters have received increasing attention. This report aims to deeply analyze the application situation and important functions of chemical filters in Fab chip wafer fabs, and provide a comprehensive reference basis for related fields through professional HVAC data analysis.
II. Special Requirements for Air Quality in the Production Environment of Fab Chip Wafer Fabs
2.1 High Requirements for Cleanliness in the Chip Manufacturing Process
Chip manufacturing is a highly precise process, involving multiple complex process steps such as lithography, etching, and deposition. In these processes, even tiny particles or chemical pollutants may have a serious impact on the performance and yield rate of chips. For example, when the line width on the chip is as small as 0.5μm, chemical pollutants in the air become one of the main harmful factors affecting the yield rate.
2.2 Hazards of Chemical Pollutants to Chip Manufacturing
There are various types of chemical pollutants in the air, such as acidic and alkaline gases (such as SO₂, NOₓ, HCl, etc.) and Volatile Organic Compounds (VOCs). These pollutants may react chemically with the chemical materials used in the chip manufacturing process, resulting in changes in the performance of photoresist, corrosion of metal lines, and a decrease in the quality of thin films, thus affecting the electrical performance and reliability of chips.
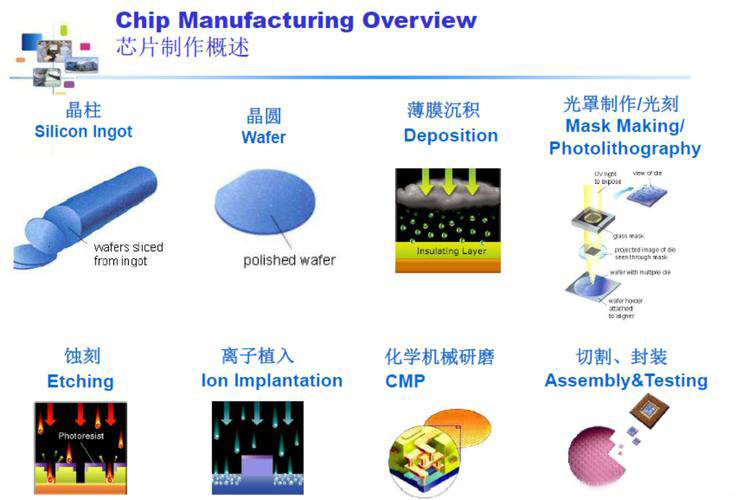
II. Special Requirements for Air Quality in the Production Environment of Fab Chip Wafer Fabs
2.1 High Requirements for Cleanliness in the Chip Manufacturing Process
Chip manufacturing is a highly precise process, involving multiple complex process steps such as lithography, etching, and deposition. In these processes, even tiny particles or chemical pollutants may have a serious impact on the performance and yield rate of chips. For example, when the line width on the chip is as small as 0.5μm, chemical pollutants in the air become one of the main harmful factors affecting the yield rate.
2.2 Hazards of Chemical Pollutants to Chip Manufacturing
There are various types of chemical pollutants in the air, such as acidic and alkaline gases (such as SO₂, NOₓ, HCl, etc.) and Volatile Organic Compounds (VOCs). These pollutants may react chemically with the chemical materials used in the chip manufacturing process, resulting in changes in the performance of photoresist, corrosion of metal lines, and a decrease in the quality of thin films, thus affecting the electrical performance and reliability of chips.
III. Working Principles and Types of
Chemical Filters 3.1 Working Principles
The working mechanism of chemical filters mainly relies on physical adsorption and chemical reactions. The following are the details of some main pollutants and their removal mechanisms:
Volatile Organic Compounds (VOCs): Removed by the physical adsorption of activated carbon.
Acidic gases (such as chlorine gas, etc.): Removed by chemical reaction neutralization, usually relying on specific chemical packing materials.
Ammonia: Removed by the chemical adsorption of acidic materials.
3.2 Types
The activated carbon materials of chemical filters are divided into granular carbon, fibrous carbon, powdered carbon, etc. Common types of chemical filters include drawer-type chemical filters, front-entry frame chemical filters (such as the frame, which integrates advanced sealing technology, is easier to update, can be updated inside the existing Air Handling Unit (AHU) system, provides space for installing plate-type and embedded modules, and provides a built-in air filter part), and ion exchange chemical filters, etc. Ion exchange chemical filters fill porous foamed materials with cation and anion exchange resins to reduce the pressure drop and increase the chance of contact with the adsorbent. Pollutants are removed through ion exchange reactions, which are effective for inorganic chemical pollution sources but not suitable for volatile organic substances. Sometimes, activated carbon filter materials need to be supplemented to form a filter material layer.
IV. Application Locations and System Configurations of Chemical Filters in Fab Chip Wafer Fabs
4.1 Application in the Air Conditioning System
In the air conditioning system of a chip factory, chemical filters are generally configured in chip production workshops where the line width is less than 0.5μm. When the air passes through the Air Handling Unit (AHU), the chemical filters can effectively remove the chemical pollutants in it, ensuring that the air supplied to the workshop meets the air quality requirements of the production process. For example, in the air conditioning systems of some large chip wafer fabs, chemical filters are installed in the intermediate and terminal filtration sections of the AHU, working in conjunction with other filtration devices such as high-efficiency filters to form a multi-stage filtration system to achieve extremely high air cleanliness standards.
4.2 Application in the Exhaust System
In order to prevent the chemical pollutants generated during the production process from accumulating in the workshop and spreading to other areas, some chip factories also use chemical filters in the exhaust system. By installing chemical filters on the exhaust ducts, the air discharged from the workshop can be purified, reducing the pollution to the external environment. At the same time, it also helps to reduce the concentration of chemical pollutants in the workshop and ensure the air quality of the production environment.
4.3 Collaborative Application with Other HVAC Equipment
Chemical filters usually cooperate closely with HVAC equipment such as fans, air ducts, and air handling units. For example, working in conjunction with the Fan Filter Unit (FFU) with its own fan, the FFU can provide the power for air flow, enabling the air to quickly pass through the chemical filter for purification treatment and then be evenly distributed to various areas of the workshop. In terms of air duct design, it is necessary to reasonably plan the air flow direction and velocity to ensure that the chemical filters can fully play their purification role, and at the same time, avoid problems such as air flow dead zones or short circuits.
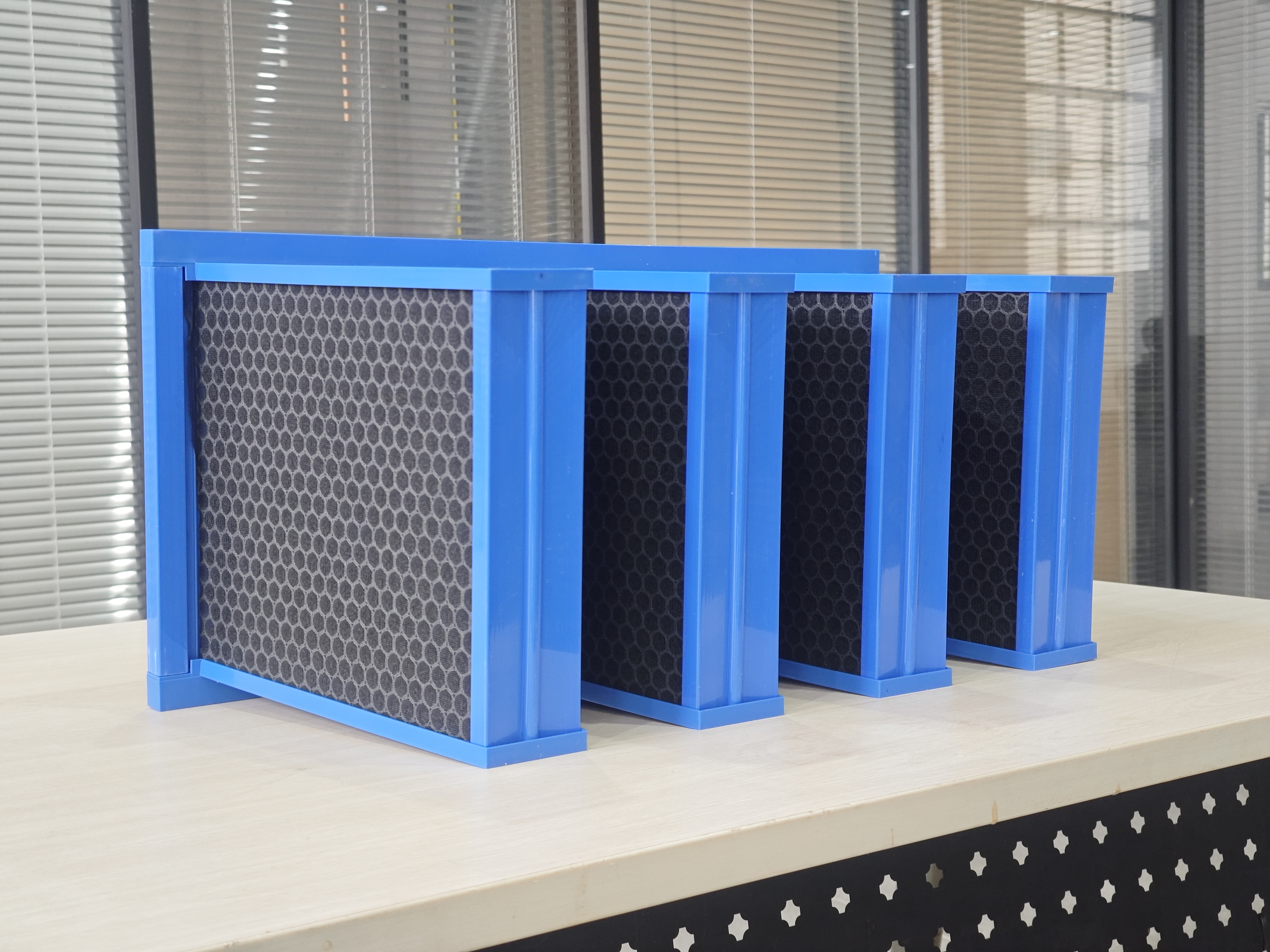
V. Analysis of the Functions of Chemical Filters in Fab Chip Wafer Fabs
5.1 Improving Product Yield Rate
By effectively removing chemical pollutants in the air, chemical filters significantly reduce the interference of pollutants in the chip manufacturing process, thereby improving the product yield rate. Relevant data shows that in a chip production workshop equipped with appropriate chemical filters, the product defect rate can be reduced by about 10% - 30%, which means a huge improvement in economic benefits for chip manufacturing enterprises.
5.2 Ensuring Stable Operation of Equipment
Chemical pollutants may cause corrosion and damage to chip manufacturing equipment, affecting the normal operation and service life of the equipment. Chemical filters can purify the air, reduce the erosion of chemical pollutants on the equipment, reduce the occurrence rate of equipment failures, and extend the maintenance cycle and service life of the equipment. For example, in a workshop without installed chemical filters, some precision lithography equipment has a relatively high frequency of failure repairs due to chemical corrosion. After installing chemical filters, the frequency of failure repairs of the equipment has decreased by 40% - 50%, greatly improving the operational stability and reliability of the equipment.
5.3 Optimizing the Production Environment
Chemical filters help maintain the stability of the air quality in the workshop, providing a healthy and comfortable working environment for operators. A good working environment can not only improve the work efficiency of employees but also reduce the risk of occupational diseases caused by air quality problems and ensure the physical health of employees. At the same time, stable air quality is also conducive to reducing the generation of static electricity in the workshop and reducing the damage to chips caused by static electricity.
5.4 Meeting Environmental Protection Requirements
Today, with the increasing awareness of environmental protection, chip manufacturing enterprises are facing strict environmental supervision requirements. The application of chemical filters in the exhaust system can effectively reduce the emission of chemical pollutants, reduce the pollution to the surrounding environment, make the production activities of enterprises comply with environmental protection regulations, and avoid legal risks and losses of corporate reputation caused by environmental problems.
VI. Performance Evaluation of Chemical Filters Based on HVAC Data
6.1 Air Volume and Wind Speed Data
By installing an air volume meter and a wind speed meter before and after the chemical filter, the air flow and velocity are monitored in real time. Reasonable air volume and wind speed can ensure that the chemical filter fully plays its purification role. Generally speaking, the face wind speed of the chemical filter in the air conditioning system of a chip factory should be controlled between 2 - 3m/s to ensure that the air has enough contact time with the adsorbent material to achieve efficient pollutant adsorption. At the same time, by adjusting the operating frequency of the fan, the air volume can be precisely controlled according to the actual needs of the workshop to meet the air quality requirements of different production processes.
6.2 Pressure Loss Data
Pressure loss is one of the important indicators for evaluating the performance of chemical filters. During the operation of the chemical filter, the pressure loss is monitored in real time through the pressure sensors installed before and after the filter. As the chemical filter is used for a longer time, pollutants will gradually accumulate on the adsorbent material, resulting in an increase in pressure loss. When the pressure loss exceeds a certain threshold, it indicates that the resistance of the chemical filter is too large, and it is necessary to clean or replace it in a timely manner. Generally speaking, the initial pressure loss of the chemical filter should be controlled between 100 - 200Pa, and when the pressure loss reaches 400 - 500Pa, it is necessary to consider maintaining or replacing the filter.
6.3 Pollutant Removal Efficiency Data
By setting gas detection instruments before and after the chemical filter, various chemical pollutants in the air are monitored in real time to evaluate the pollutant removal efficiency of the chemical filter. Different types of chemical filters have different removal efficiencies for different pollutants. For example, for common acidic gases (such as SO₂), the removal efficiency of high-quality chemical filters can reach more than 90%; for Volatile Organic Compounds (VOCs), the removal efficiency can also reach about 70% - 80%. Through the analysis of pollutant removal efficiency data, the performance status of the chemical filter can be known in a timely manner, providing a basis for the selection and optimization of the filter.
6.4 Temperature and Humidity Data
Temperature and humidity also have a certain impact on the performance of chemical filters. In the chip factory workshop, temperature and humidity sensors are installed to monitor the changes in environmental temperature and humidity in real time. Generally speaking, chemical filters can maintain good performance in an environment with a relative humidity of 30% - 60% and a temperature of 20 - 25℃. Too high or too low temperature and humidity may affect the activity and adsorption effect of the adsorbent material, resulting in a decrease in the purification efficiency of the chemical filter. Therefore, it is necessary to precisely control the temperature and humidity in the workshop through the HVAC system to ensure that the chemical filter is always in the best working state.
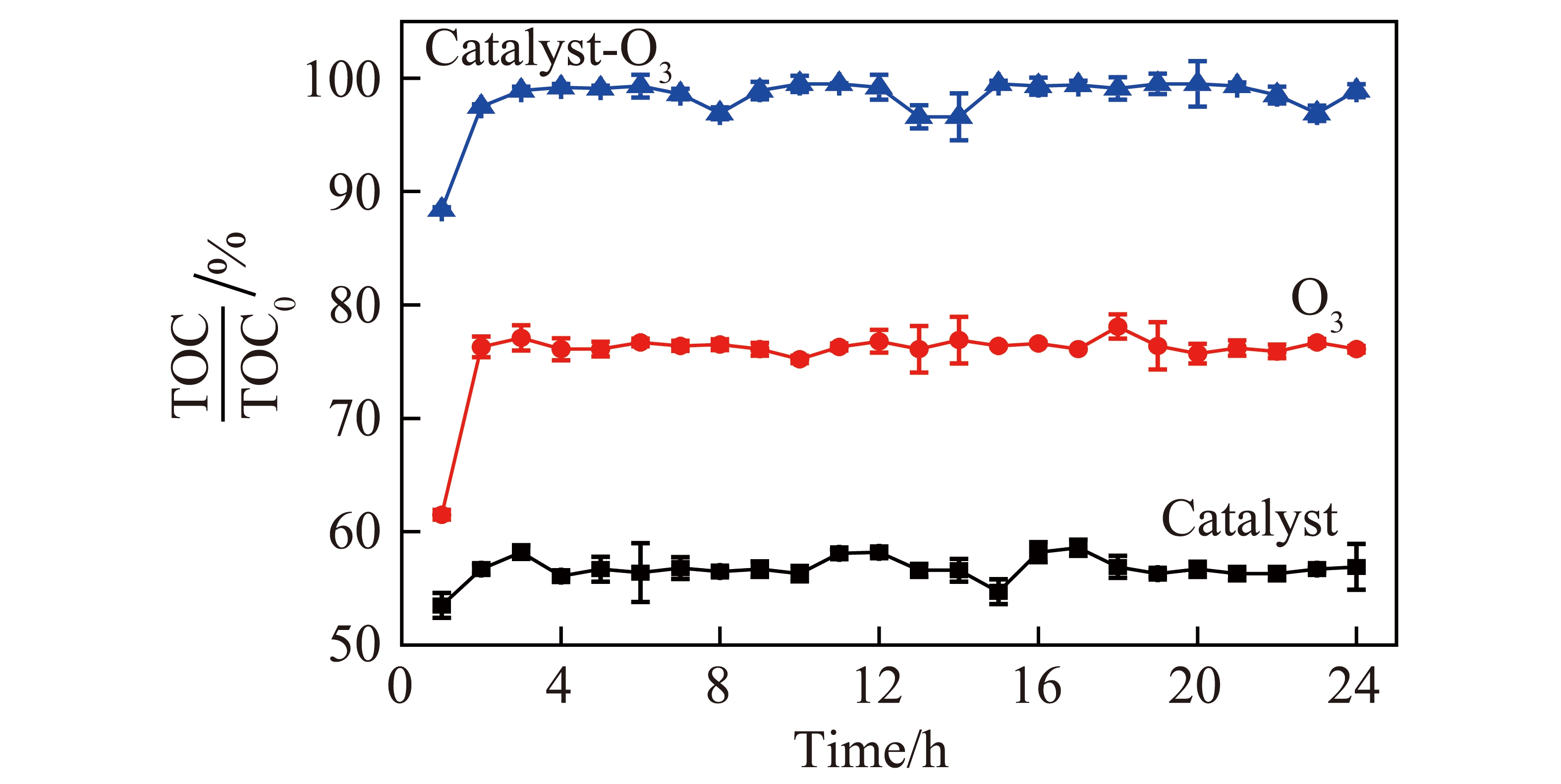
VII. Selection and Maintenance Suggestions for Chemical Filters
7.1 Selection Suggestions
When selecting chemical filters, factors such as the production process requirements of the chip factory, the air quality status, the types and concentrations of chemical pollutants need to be comprehensively considered. First, select the appropriate adsorbent material and filter type according to the types of chemical pollutants in the workshop. For example, if there is mainly acidic gas pollution in the workshop, a chemical filter with high adsorption capacity for acidic gases should be selected; if the content of Volatile Organic Compounds (VOCs) is high, a filter specifically designed for the removal of VOCs is required. Second, select the appropriate specification of the chemical filter according to the air volume and filtration area requirements to ensure that it can meet the air purification needs of the workshop. In addition, factors such as the brand, quality, price, and after-sales service of the filter should also be considered, and a product with high cost performance should be selected.
7.2 Maintenance Suggestions
In order to ensure that the chemical filter always maintains good performance, regular maintenance is essential. Regularly check the appearance of the chemical filter to see if there is any damage or deformation; regularly clean the filter to remove the dust and impurities on the surface, and methods such as vacuuming or washing with water can be used, but care should be taken to avoid damaging the adsorbent material. At the same time, according to the pollutant removal efficiency and pressure loss data, replace the adsorbent material or the entire filter in a timely manner. Generally speaking, the service life of the adsorbent material of the chemical filter is about 6 - 12 months, and the specific replacement cycle should be determined according to the actual use situation. In addition, establish a complete maintenance record file, recording information such as the installation time, maintenance time, maintenance content, and replacement situation of the chemical filter to track and analyze the operation status of the filter.
VIII. Case Analysis of the Application of Chemical Filters
8.1 Case 1: A Large Chip Wafer Fab
Taking an internationally renowned semiconductor factory as an example, the factory introduced advanced chemical filter technology in the HVAC system. Through continuous data monitoring and maintenance, the cleanliness of the manufacturing environment has been significantly improved, resulting in a 15% increase in the product yield rate. The success of this case reflects the importance and necessity of chemical filters in modern Fabs. In the newly built advanced process workshop of the chip wafer fab, high-performance chemical filters were fully adopted. In the air conditioning system, multi-stage chemical filtration modules were configured, including primary, intermediate, and high-efficiency chemical filters, which respectively removed chemical pollutants of different particle sizes and properties. According to real-time monitoring data, after installing the chemical filters, the concentration of chemical pollutants in the workshop was significantly reduced. For example, the concentration of SO₂ decreased from the original 50ppb to below 5ppb, and the concentration of VOCs decreased from 100ppb to about 20ppb. At the same time, the product yield rate was greatly increased, from the original 80% to more than 90%, and the frequency of equipment failure repairs was also significantly reduced, achieving remarkable economic and environmental benefits.
8.2 Case 2: A Small and Medium-sized Chip Factory
A small and medium-sized chip factory added chemical filters during the renovation of the original workshop. Due to limited budget, the factory chose a combination of ion exchange chemical filters and activated carbon filters with relatively high cost performance. After installing the chemical filters, through the monitoring of the air quality in the workshop, it was found that the removal effect of inorganic chemical pollutants was good, and the concentration of acidic and alkaline gases in the workshop was effectively controlled. At the same time, the operators reported that the smell in the workshop was significantly improved, and the working environment was more comfortable. Although the increase in the product yield rate was relatively small (from 75% to about 80%), it also improved the production efficiency and product quality to a certain extent.
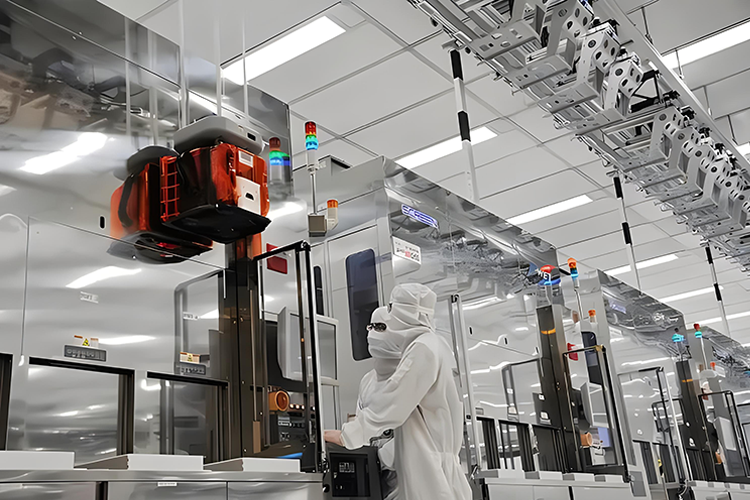
IX. Conclusions and Prospects
The application of chemical filters in Fab chip wafer fabs is of inestimable value for ensuring product quality, improving production efficiency, and maintaining the safety of employees. With the continuous progress of the semiconductor industry, future chemical filters will be more intelligent and automated; their performance and applications will also be continuously optimized and improved, providing more efficient air purification solutions for the sustainable development of wafer fabs.
This article has deeply discussed the functions of chemical filters in Fab chip wafer fabs, hoping to provide a reference for research and practice in related fields. In the increasingly strict market environment, improving air quality management will be an important measure to maintain the competitiveness of enterprises.